For dosing Gases in a vacuum chamber there are different approaches.
With an Upstream – Control: the pressure inside the chamber is controlled with a Valve at the inlet, while wirh a Downtstrem Control the Valve is directly above the pump. The Advantage of the Upstream – Control is the lesser gas consumption. Also there is no Need for a throttle. The following picture Shows the difference:
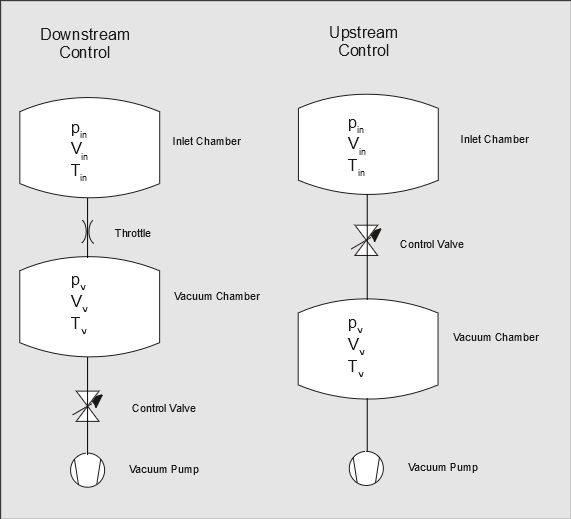
The shown system is an abstracted part of a real vacuum system. The differences are:
- the inlet and inlet state of the gas with the variablves pressure, temperature and volume. In a real system different conditions can be realized by cutting-off or adding additional chambers.
- the vacuum pump system, which may be composed of some pumps and bypass lines to accomplish different gas states
- different interfaces at the chamber, in which the vacuum shall be controlled. These can be on/off locks to bring in or out materials ar Manipulators to process materials.
For modeling the Control the inlet will be represented by the state variables pressure, temperature and volume.
The vacuum pump system will be represented by the pump prperties: suction power, püumping Speed and end pressure.
The possibly existing interfaces on the vacumm chamber will be ignored. It is assumed, that the components are sufficiently tight to reach the required end pressure. Therefore the chamber will be assumed as completely tight.
The Control Valve will be given: the nenion steppermotor driven gas dosing valve.